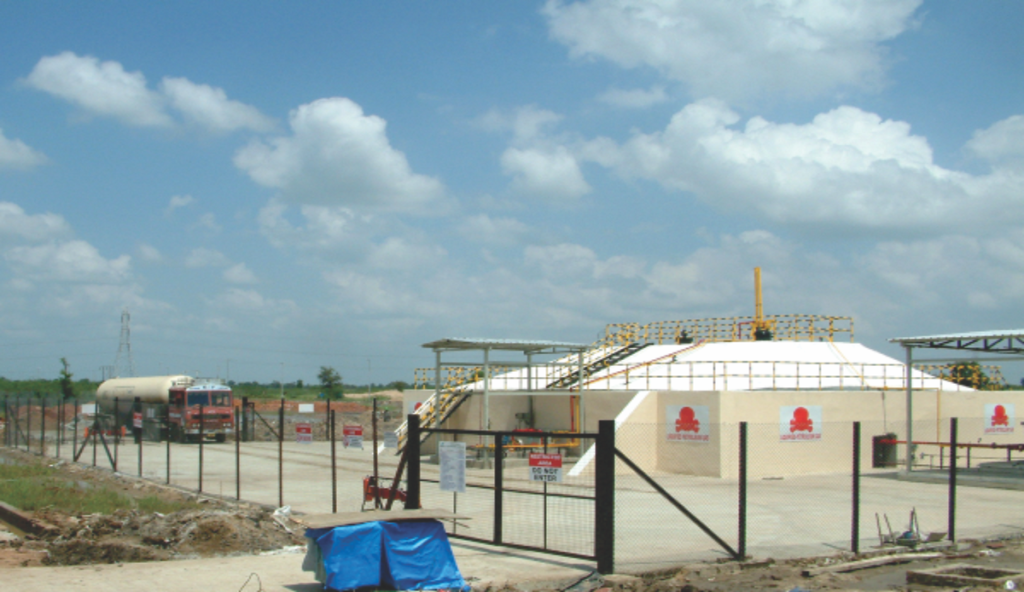
LPG/PROPANE PLANT INSTALLATION:
Design, manufacturing and installation for a range of LPG/PROPANE storage solutions that cater to the requirement of various industries such as ceramic, glass, steel, auto etc., KEW has years of experience in plant installation for LPG/PROPANE.
LPG/PROPANE – Over ground installation, mounded installation, pipeline work
Installing an LPG (Liquefied Petroleum Gas)/PROPANE plant involves several crucial steps to ensure safety, efficiency, and compliance with regulations. Here’s an outline of the typical contents involved in the installation process:
- Site Selection and Preparation:
- Identifying a suitable location for the plant, considering factors like proximity to consumers, safety regulations, and accessibility for transportation.
- Conducting feasibility studies to assess the environmental impact, zoning regulations, and infrastructure requirements.
- Regulatory Compliance:
- Obtaining necessary permits and licenses from local, state, and national regulatory bodies.
- Adhering to safety standards such as those set by OSHA (Occupational Safety and Health Administration) and NFPA (National Fire Protection Association).
- Engineering Design:
- Collaborating with engineering firms to design the layout of the plant, including storage tanks, pipelines, safety systems, and processing equipment.
- Ensuring the design meets safety codes and standards, considering factors like pressure ratings, material compatibility, and emergency shutdown procedures.
- Procurement of Equipment and Materials:
- Sourcing high-quality equipment, such as storage tanks, compressors, valves, and instrumentation, from reputable suppliers.
- Ensuring that all materials meet regulatory standards and specifications.
- Construction and Installation:
- Excavation and preparation of the site for laying foundations and installing equipment.
- Erecting storage tanks, piping systems, compressors, safety devices, and other components according to the engineering design.
- Conducting quality inspections and tests at each stage of construction to ensure compliance with specifications and safety standards.
- Safety Systems and Emergency Preparedness:
- Installing safety systems such as leak detection, fire suppression, and emergency shutdown systems.
- Training personnel on safety procedures, emergency response protocols, and the proper handling of LPG.
- Commissioning and Testing:
- Conducting thorough testing and commissioning of all equipment and systems to ensure they operate safely and efficiently.
- Performing pressure tests, leak tests, and functional tests to verify the integrity and performance of the plant.
- Training and Documentation:
- Providing comprehensive training to plant operators and maintenance staff on operating procedures, safety protocols, and maintenance requirements.
- Documenting all aspects of the installation, including design drawings, equipment manuals, safety procedures, and inspection records.
- Start-Up and Operation:
- Gradually ramping up production and monitoring the plant’s performance during initial operation.
- Implementing regular maintenance and inspection schedules to ensure the ongoing safe and efficient operation of the plant.
- Continuous Improvement and Compliance:
- Regularly reviewing and updating safety protocols, operational procedures, and maintenance practices to improve efficiency and ensure compliance with evolving regulations.
- Conducting periodic audits and inspections to identify potential hazards, address safety concerns, and maintain regulatory compliance.